Rubber expansion joints cause force on the adjacent sliding or fixed points when under pressure (active bellows cross-section surface area x operating pressure). The force created by this pressure is designated as pressure thrust.
Where the pipe supports are not designed to absorb this force, tie-rods must be incorporated across the joint from flange to flange so that the expansion joint is restrained in axial direction and can move lateral only. It can be eliminated also by using angular expansion joints with hinges and pin, such that the pipe anchors and guides are unburdened accordingly.
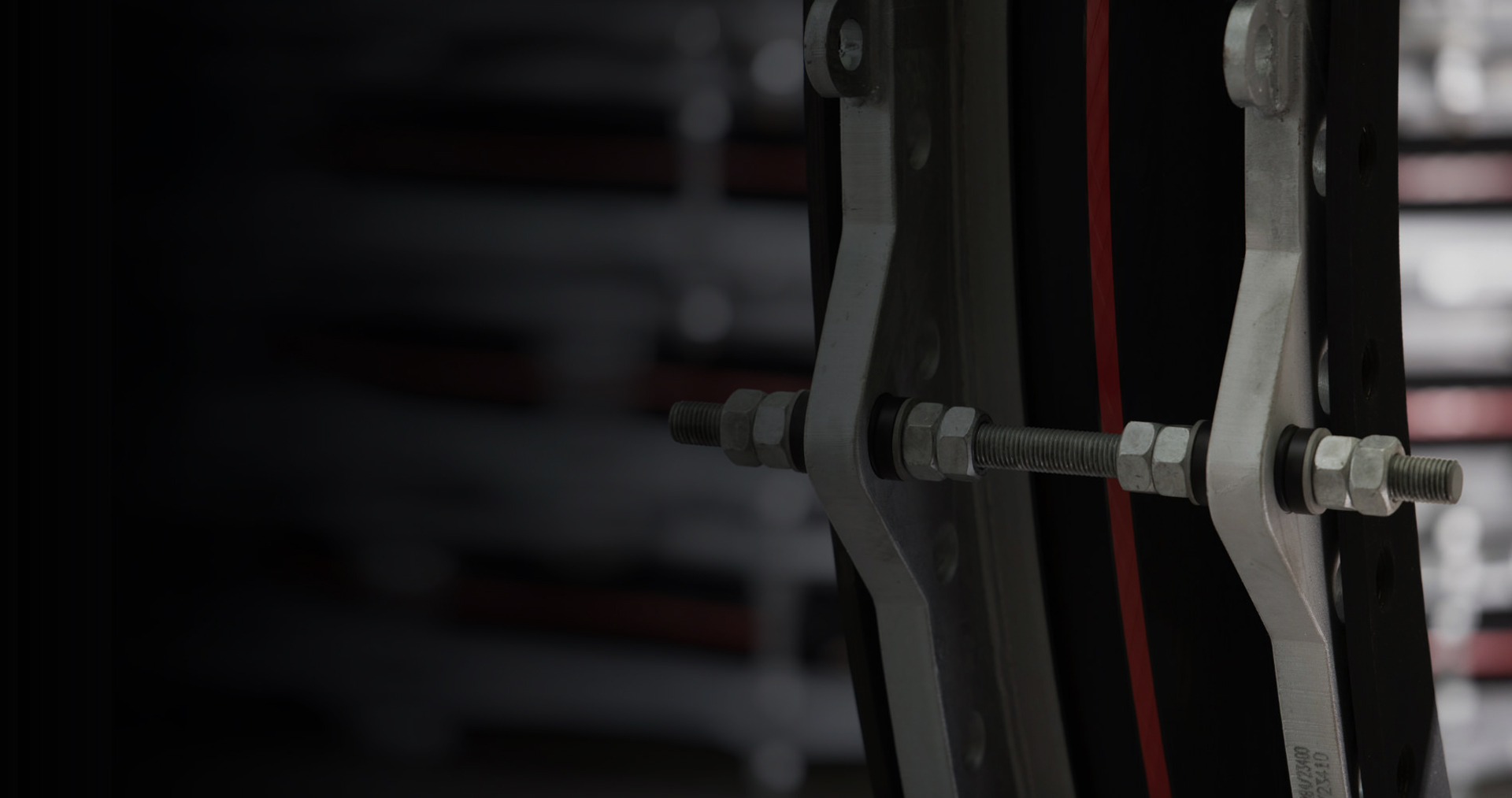
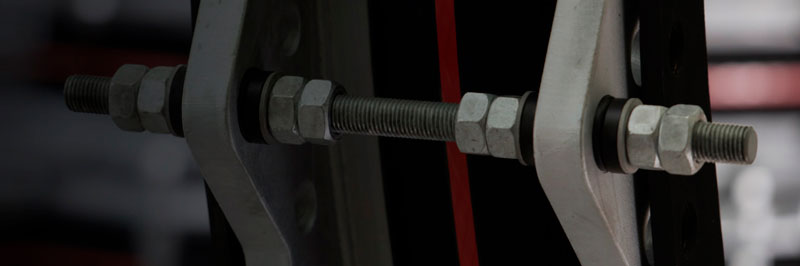