Fabric expansion joints are specially designed and dimensioned for each application with regard to the operating conditions in question. In addition to the dimensions, we need information about the medium, temperature, pressure and movements. The pipeline expands at operating temperature. Depending on the configuration of the fixed and sliding points, such stretching is accommodated by the expansion joint in an axial, lateral and/or angular direction. The thermal expansion must be determined when planning the pipeline, and will influence the choice of expansion joint construction shape as well as the choice of optimal installation length.
Design Criteria
- Design Criteria
- Medium
- Temperature
- Pressure
- Movements
The exact operating parameters and constraints are needed to design the expansion joint. Temperature information that is higher than actual operating temperatures may lead, for instance, to the expansion joints being designed with unnecessary insulating layers, which has an unfavorable effect on pressure tightness in the fixing area.
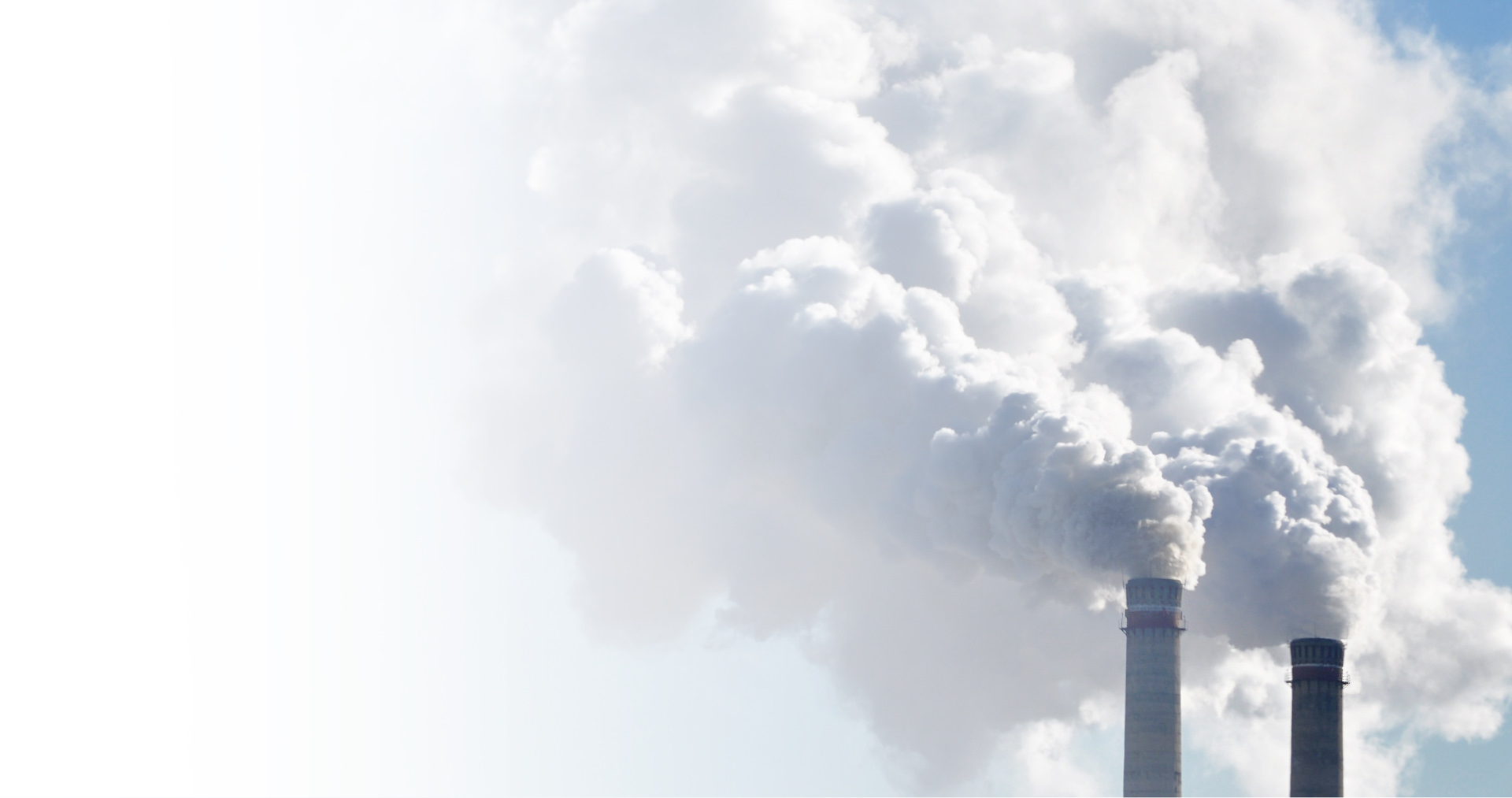
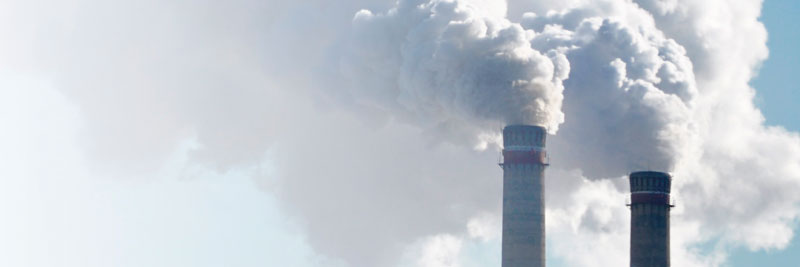
The medium, in conjunction with the operating temperature and operating pressure, determines which material is selected for the construction of the expansion joint.
The following media properties should be taken into account:
- Crude or scrubbed gases
- Solid fraction (load and particle size)
- Chemical composition (acids, bases, solvents, radiation)
- Flue gas from coal, oil or gas firing
- Dry or wet medium
- Duct rinsing or cleaning
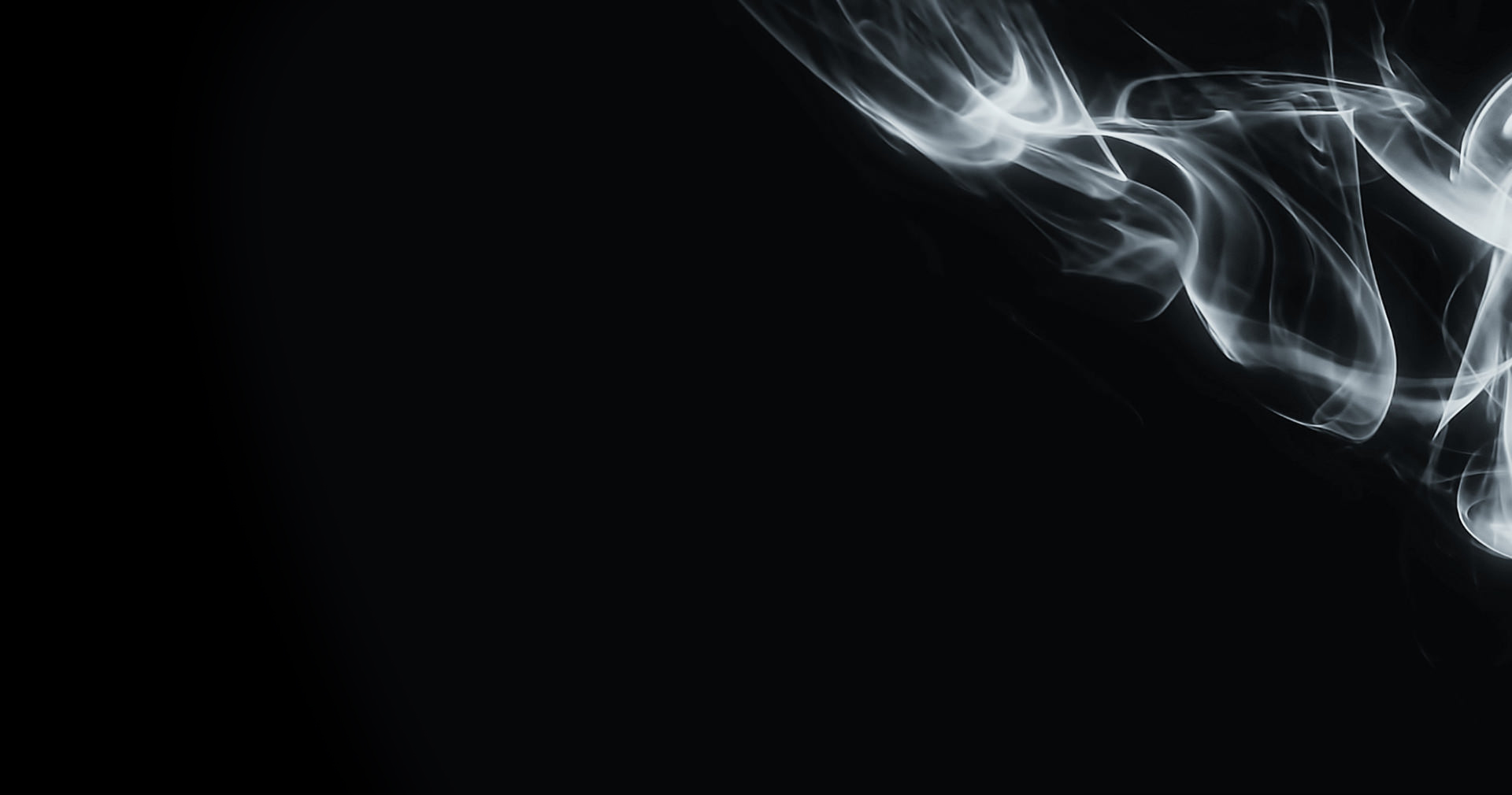
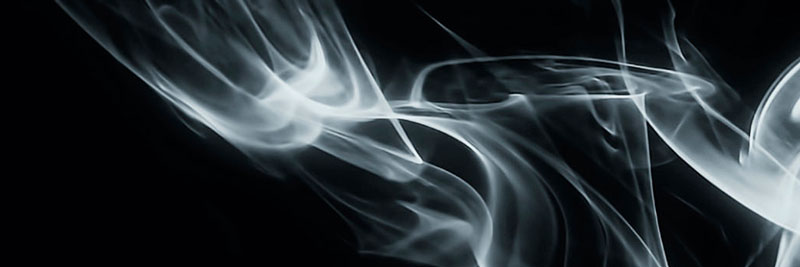
In addition to the operating temperature, it is important to know the maximum possible temperature in the event of an accident or the design temperature when selecting the bellows material. The medium temperature also determines whether the expansion joint can be installed at the duct level or if a duct angle needs to be used to establish a distance from the hot medium. In the event of a high ambient temperature, e.g. in the vicinity of a boiler or for expansion joints in housings, this also constitutes a design criterion.
If there is a risk of falling below the dew point and for medium temperatures of up to 220 °C, we recommend insulating the expansion joints from outside. Otherwise condensation may form and corrode the duct or lead to leaks in the expansion joint connection area. Since condensation constitutes yet another chemical strain, forecasted situations where the temperature might fall below the dew point must be specified, especially in the event of process-dependent start-up or shut-down or in the event of partial load operation. Dew point shortfalls influence the design of the expansion joint as well as the selection of the construction material.
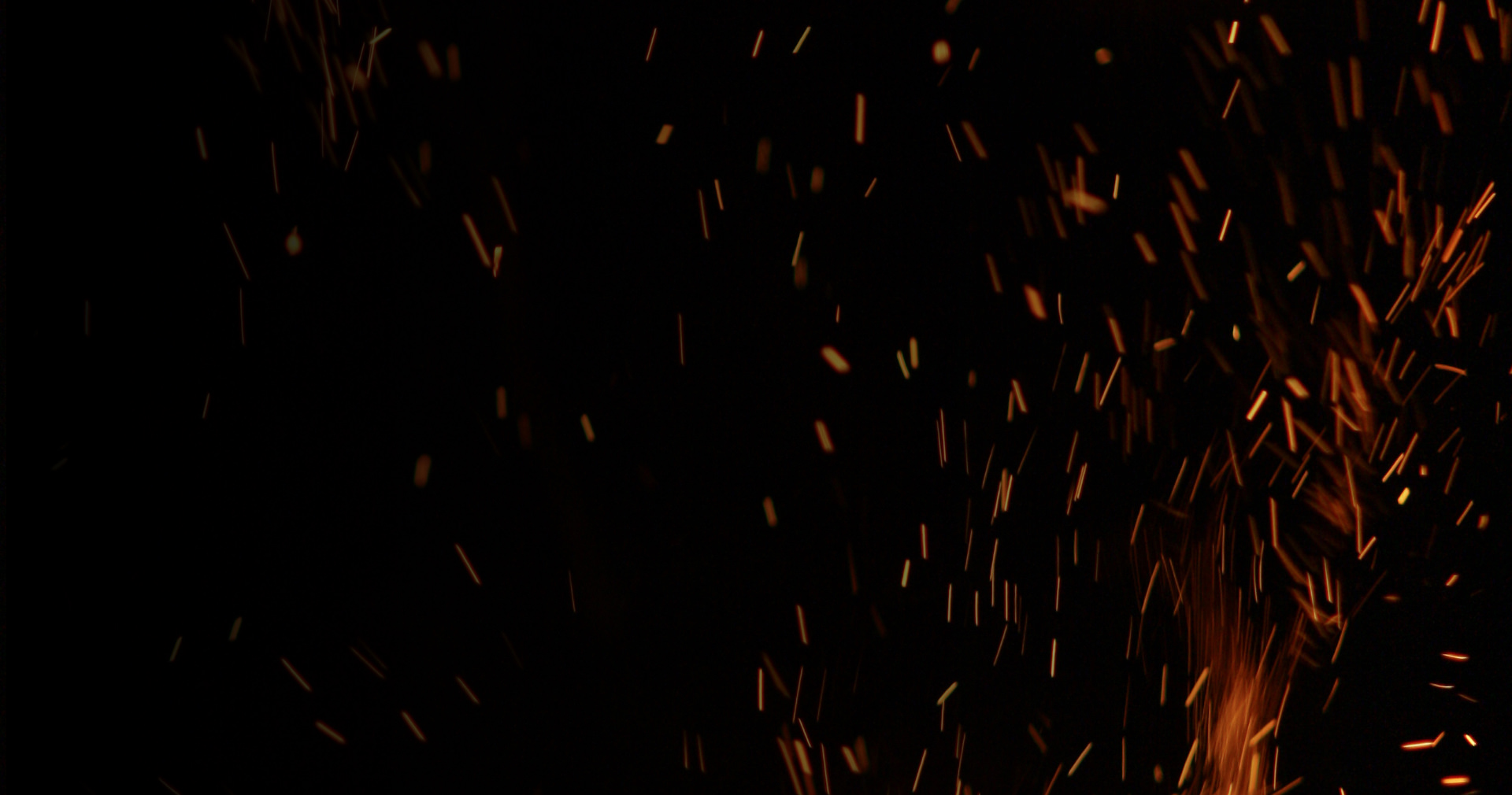
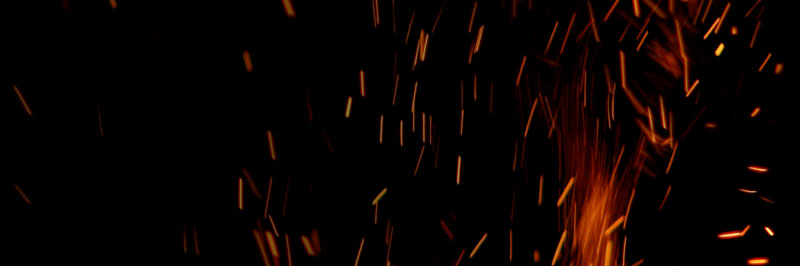
In addition to temperature, pressure determines both the material and the design of the expansion joint. For high pressure, we recommend using flange expansion joints, since these can handle high pressure-tightness requirements as a result of their clamping.
You should also check whether additional design measures are needed, such as the use of pressure support rings or vacuum support rings. If pressure oscillations or pressure surges are anticipated, please specify them.
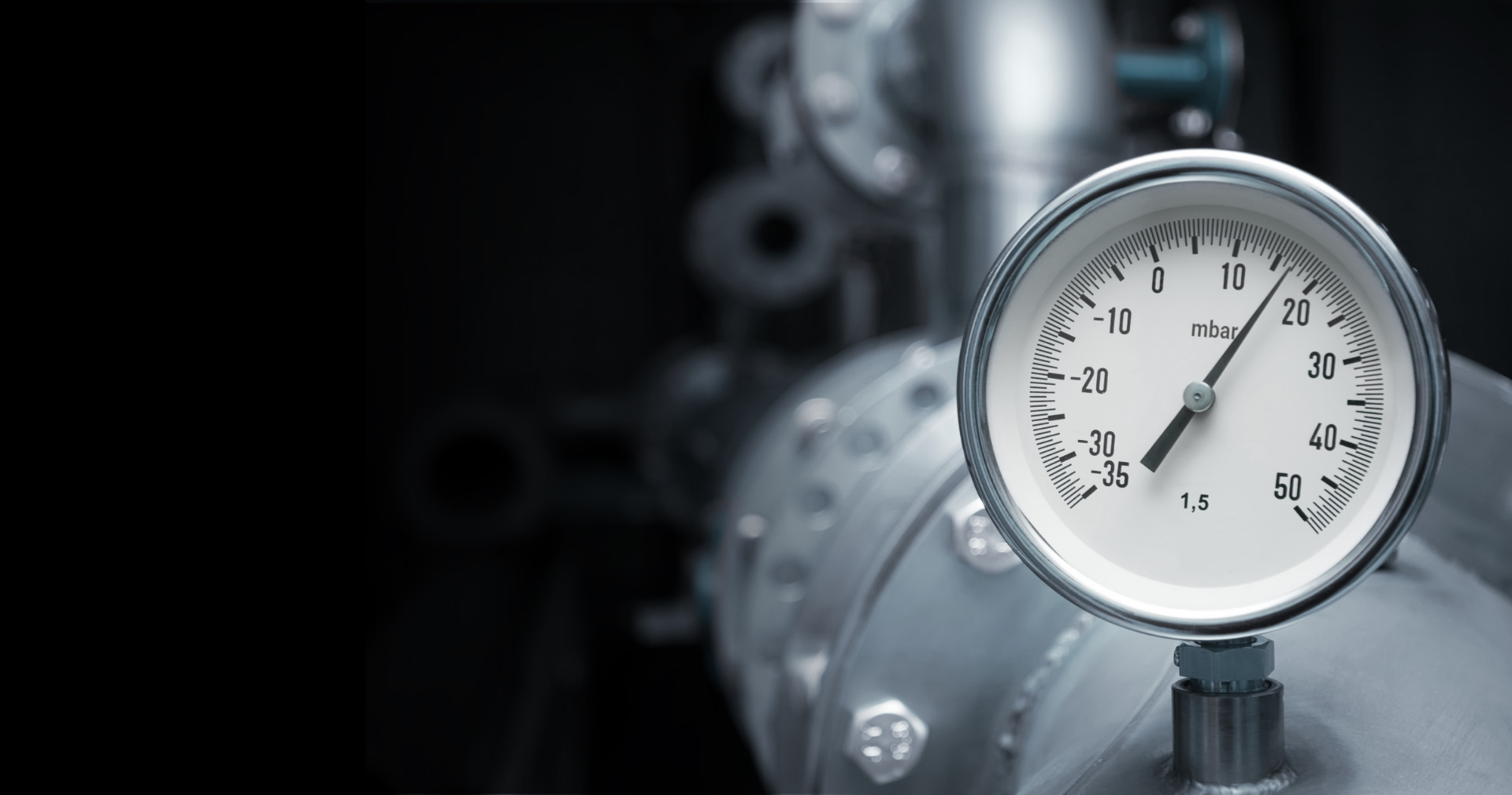
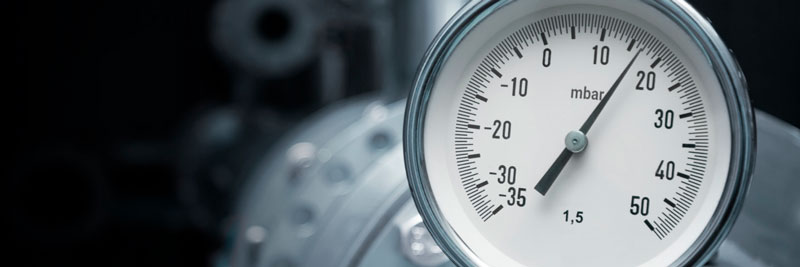
Depending on the type, fabric expansion joints can accommodate large movements in an axial, lateral or angular direction. Axial and lateral movement mostly occur in combination, and it is important to know which movement will occur first during start-up or shut-down. The movements to be accommodated determine the design and the installation gaps to be used for the expansion joint. Large movements can be distributed across several expansion joints in some cases.
Bellows Construction
- Bellows Construction
- Elastomer Expansion Joints
- Multilayer Expansion Joints
- Tightness
For fabric expansion joints, there are no stiffness rates acting on the adjacent ducts, contrary to steel or rubber expansion joints. These need comparatively little installation space even for large movements.
Each fabric expansion joint is individually adapted to the conditions, and our technicians decide whether to use an elastomer or multilayer expansion joint when preparing a quotation.
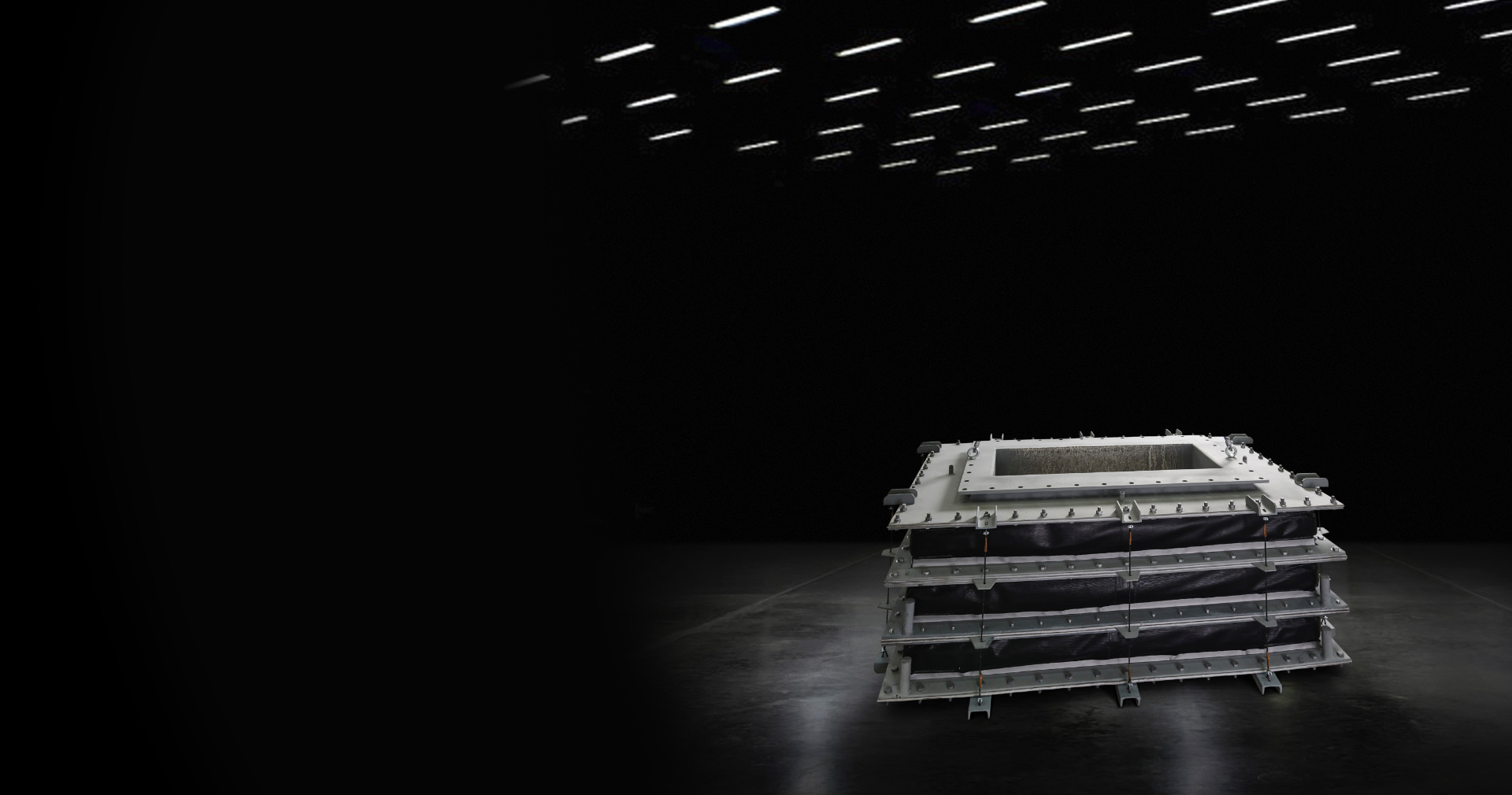
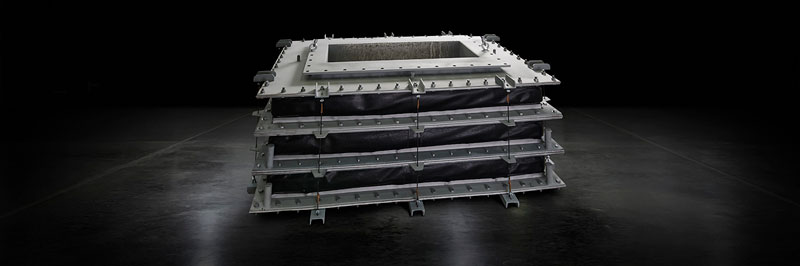
This is a single-layer expansion joint made from rubber, approx. 3 to 6 mm thick, with one or more reinforcement carriers. Elastomer expansion joints are characterized by their gas-tightness and drip-tightness, even if there is condensation. The maximum deployment temperature is 200 °C. The choice of rubber grade depends on the operating temperature and the medium. This decision is made on the basis of our extensive experience and with regard to relevant durability tables.
The following table provides an overview of the elastomers we handle. For the most corrosive media, we can furnish the expansion joint with an additional interior PTFE lining, which is firmly joined to the rubber bellows. PTFE is resistant to a number of chemicals and to many different mixtures, and can for that reason be used in the event of corrosive chemical attack.

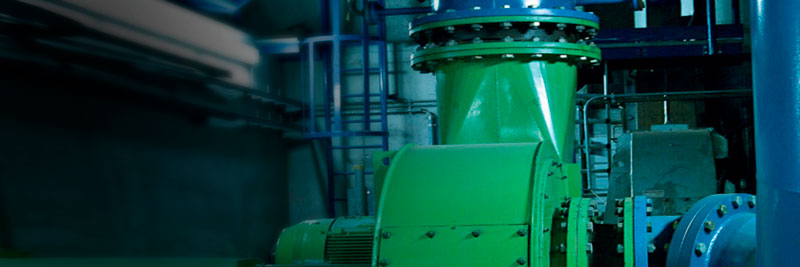
These consist of one or more superimposed insulating layers, a chemically resistant sealing film, and an external skin that ensures that the expansion joint maintains its shape under pressure.
For simple applications, single-layer expansion joints are used. In general, these consist of a thin rubber or PTFE film with a fabric reinforcement.
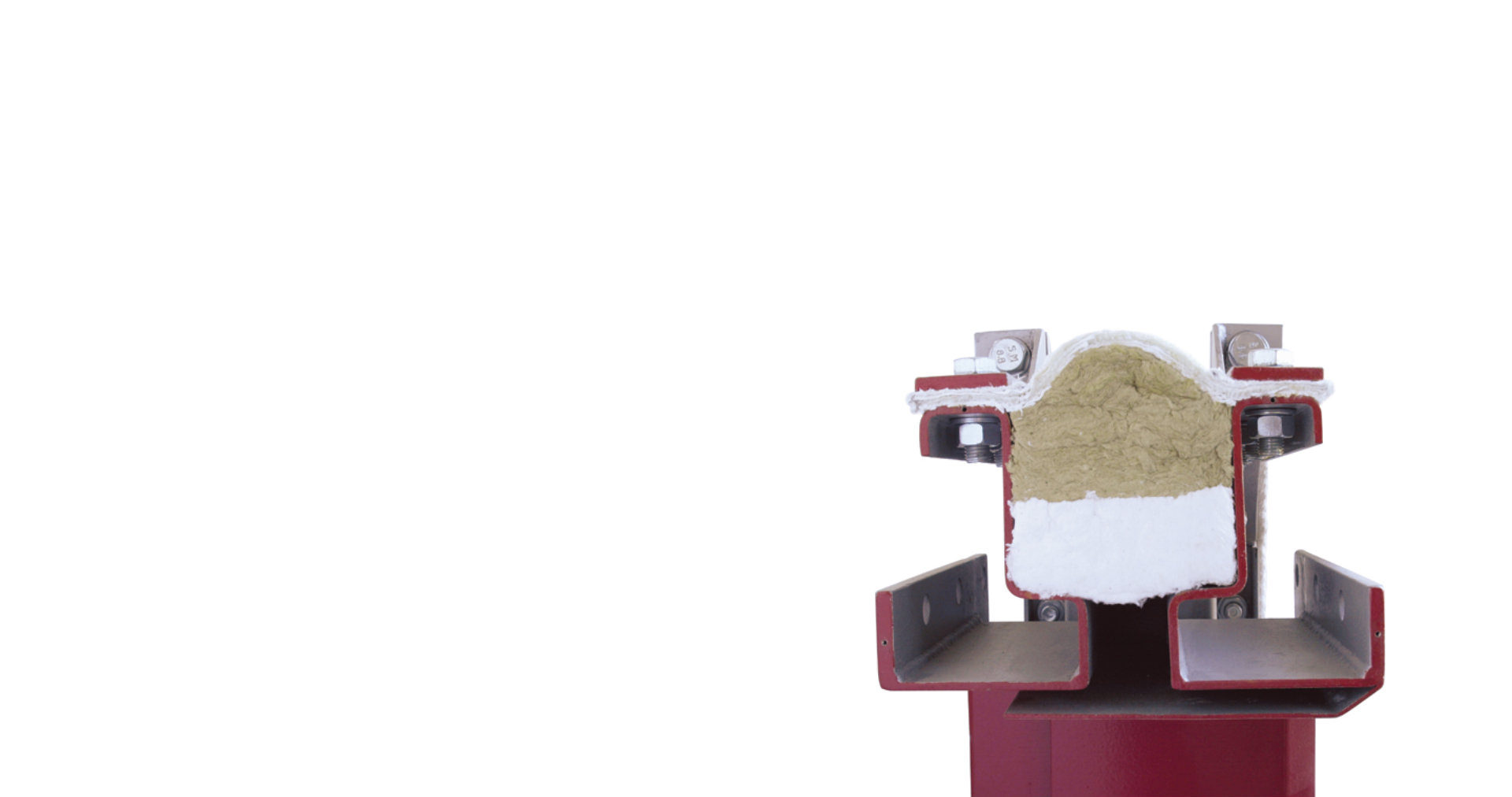
Expansion joints with a wall thickness of up to 6 mm and for an operating pressure of up to 0.3 bar are elastomer expansion joints. These are gas-tight and drip-proof. Rubber expansion joints are used at higher pressure.
In multilayer expansion joints, the inner insulating layers in the clamping area lead to marginal diffusion. The bellows itself is gas-tight as a result of its sealing layer. Multilayer expansion joints are therefore only considered impermeable to flue gas, whereas elastomer expansion joints are impermeable to bubbling agent. Multilayer expansion joints are not impermeable to drips, and precautions may have to be taken in the design phase. Up to 220 °C, multilayer expansion joints can be manufactured for highly gas-tight requirements. These are furnished with an inner layer of PTFE-coated glass fiber fabric that is then sealed using a PTFE sealing belt or a temperature-resistant rubber seal against the duct flange. In this case, these seals are attached to the expansion joint at the factory.
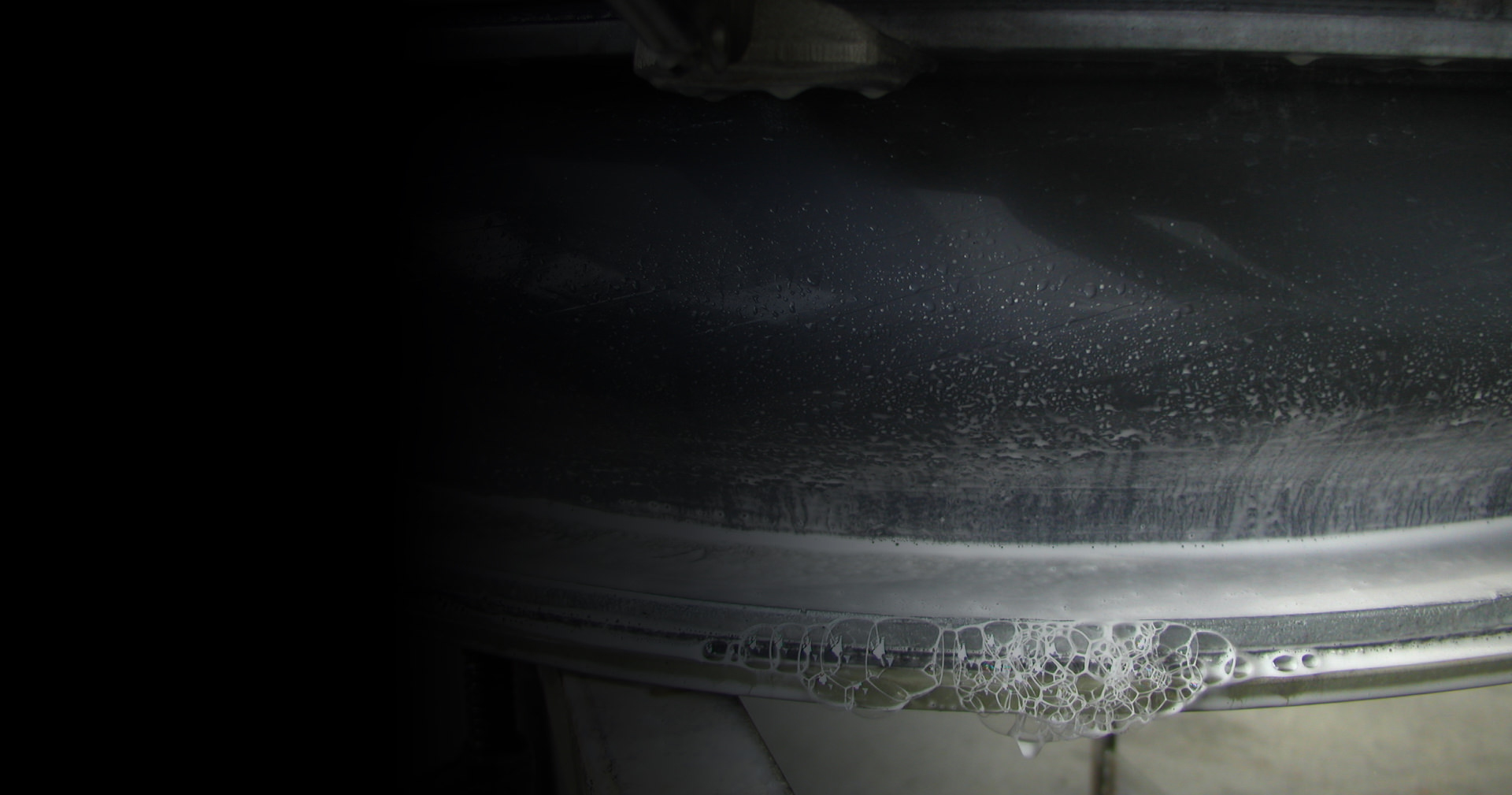
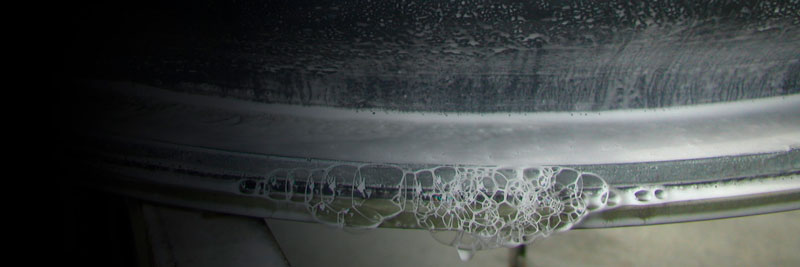
Fixing Types
- Fixing Types
The distance between the ends of the pipeline and the duct flanges or duct angles is dependent on the axial and lateral movements. Guideline values for determining the installation gaps can be found under the respective expansion joint types.
In principal, the expansion joint should only be compressed or displaced by a quarter of its original installation length, since extreme compression can lead to buckles, and thus also to heat pockets and overheating. Our technicians will be happy to help you determine the optimal installation gap.
Explore Flange Expansion Joints Explore Belt Expansion Joints
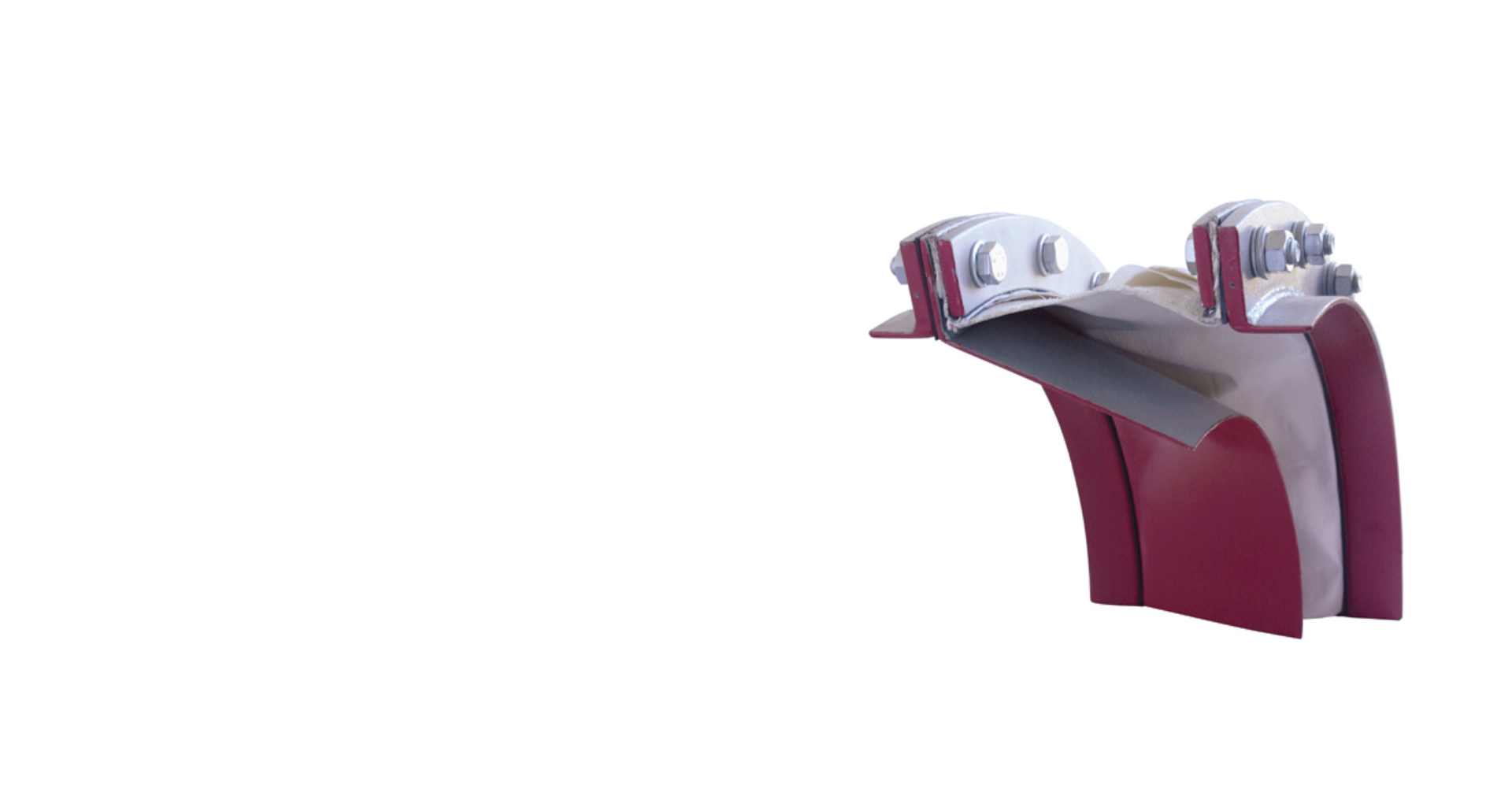
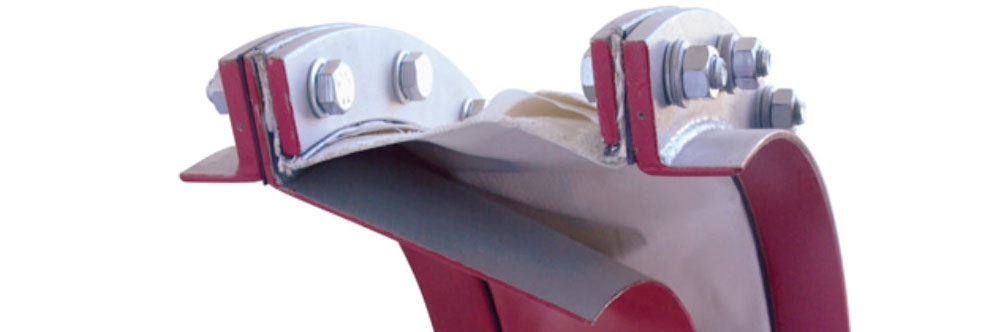
Insulation Technology
- Pre-insulation
- External Insulation
Pre-insulation reduces the medium temperature up to the expansion joint bellows and protects it against dust. It also supports the expansion joint in the event of pressure variations, and contributes to sound insulation.
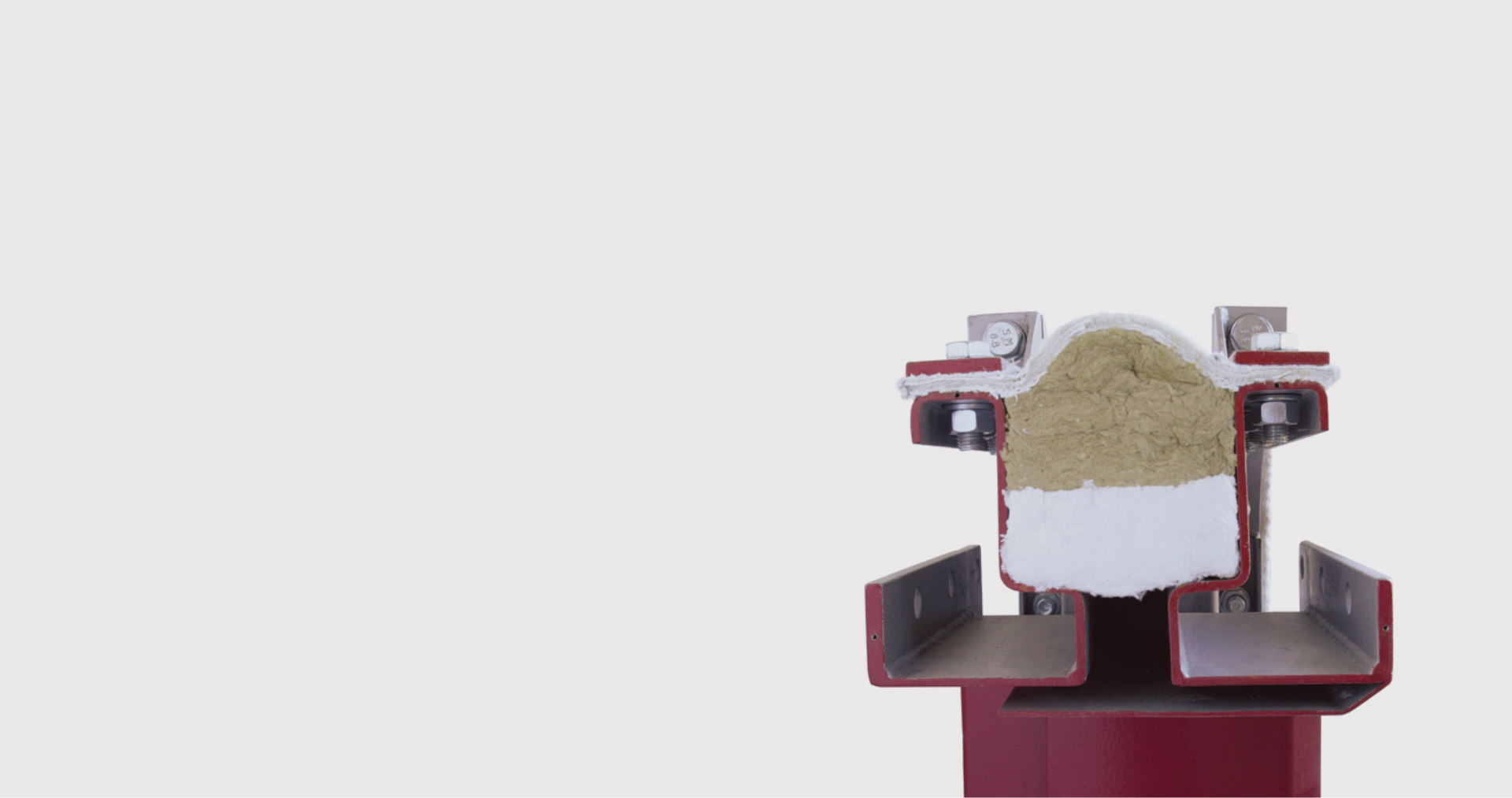
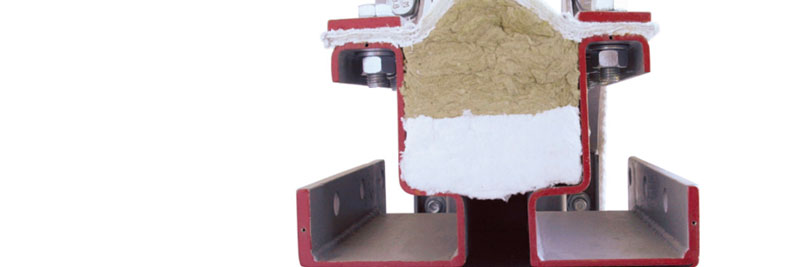
If there is a risk of falling below the dew point and for medium temperatures of up to 220 °C, we recommend insulating the expansion joints from outside. Otherwise condensate may form and corrode the duct or lead to leaks in the expansion joint connection area. For temperatures over 220 °C, the expansion joint may in no event be insulated from the outside, since the expansion joint’s convection would otherwise no longer be assured.
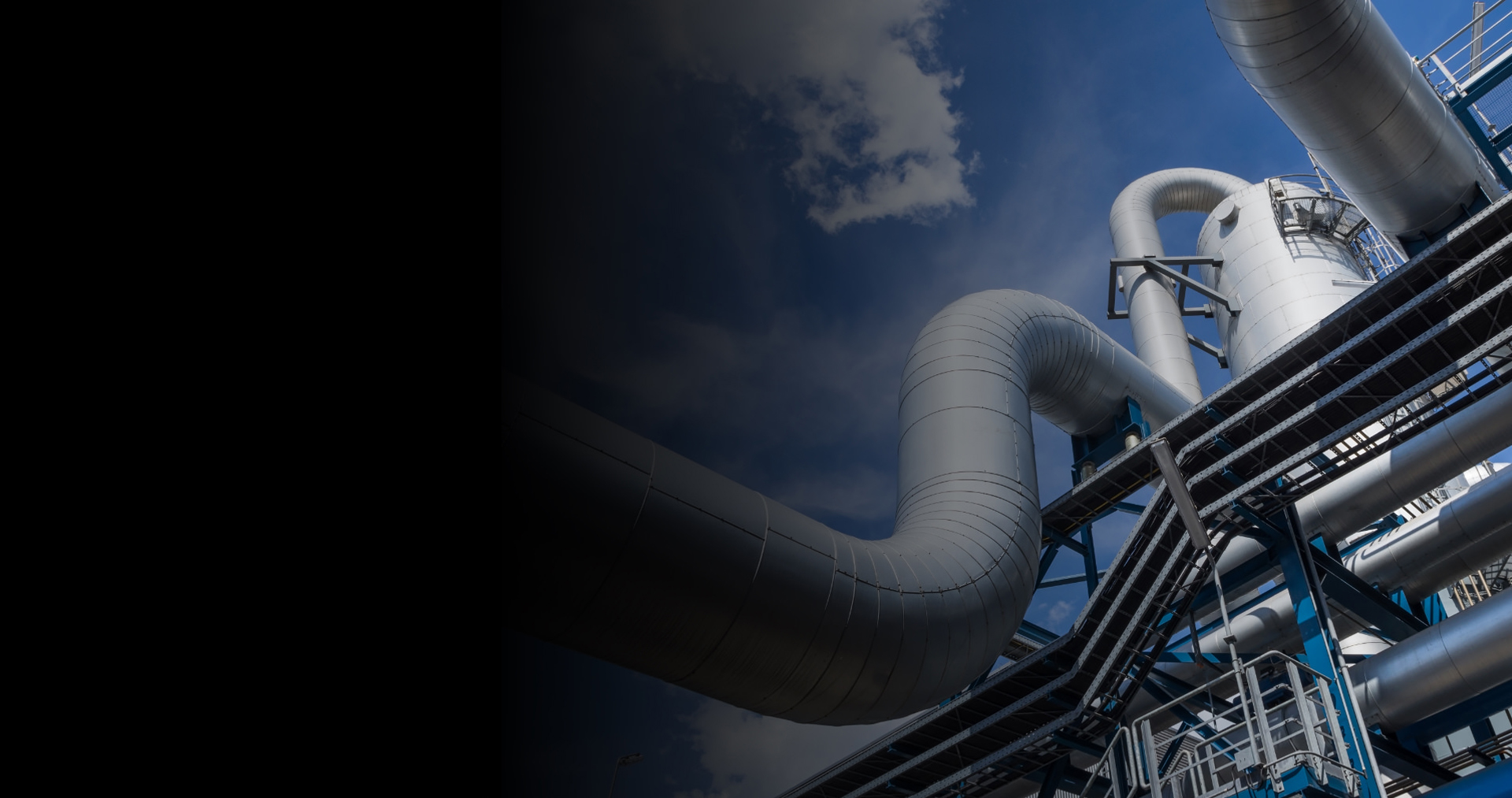
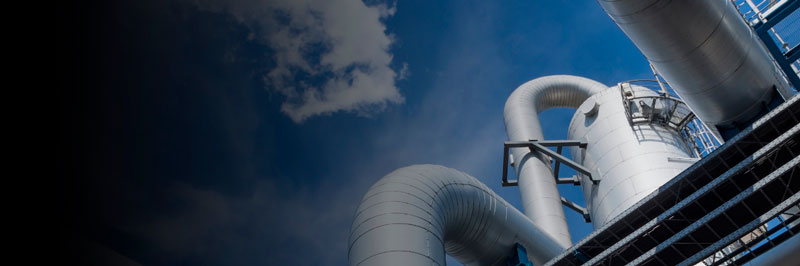
Flow Liners
- Flow Liners
Flow liners should be used if the flow rate is greater than 30 m/s or if there are solids present in the medium. Flow liners are also used if the expansion joint has been installed immediately after a change in the direction of the duct. For horizontal ducts and vertical ducts with a media flow from the top down, the flow liners are installed in the direction of flow.
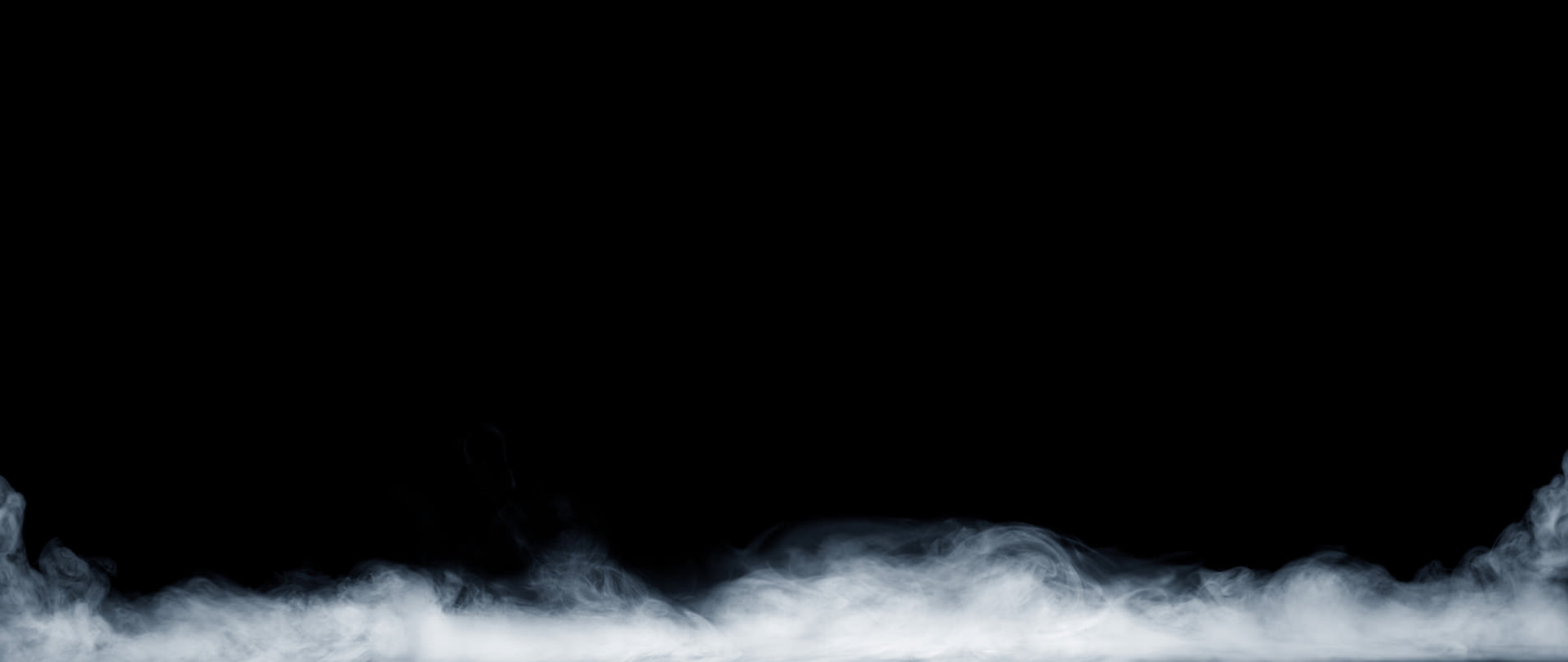
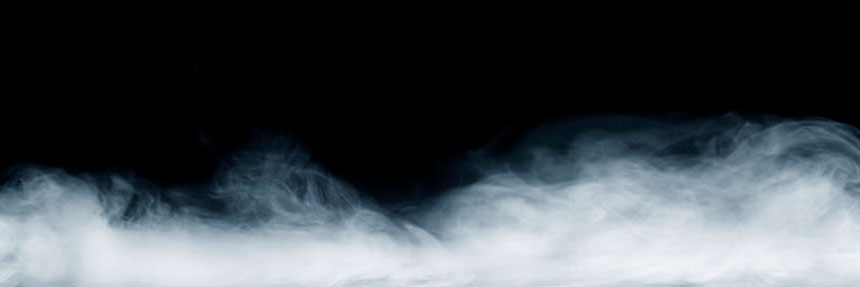
Accessories
- Fixing Elements
- Installation Unit
- Installation Set
Flange expansion joints are fixed using backing flanges on the duct flange. For belt expansion joints installed directly onto the line, clamps are used. If a duct angle is necessary, the expansion joints are pressed onto the angle flange using clamp bars.
In order to keep the pressure of the backing flange or clamp bar constant when the system is at high temperature, disc spring packets can be used. If needed, we can deliver all necessary fixing elements as accessories.
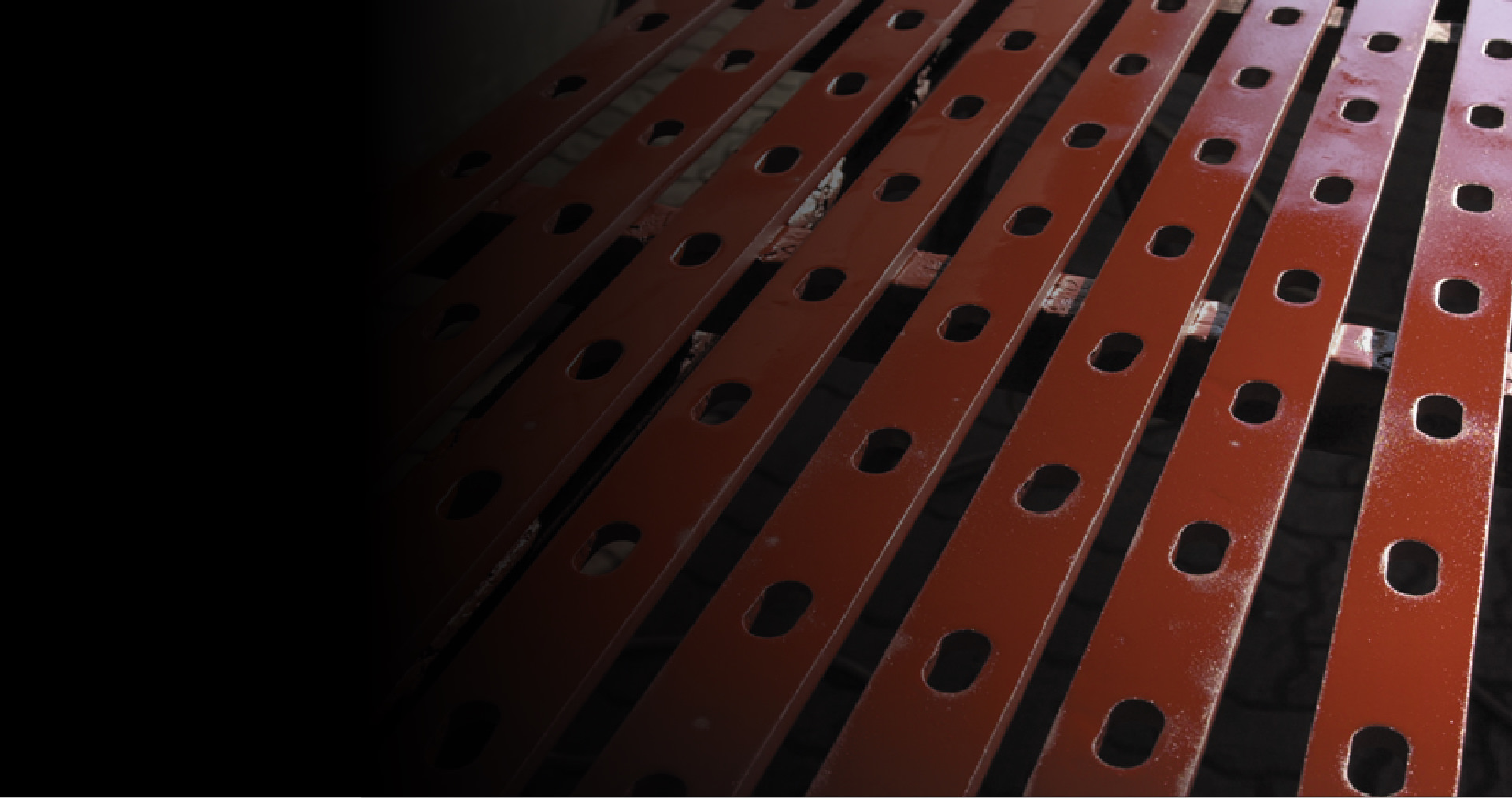
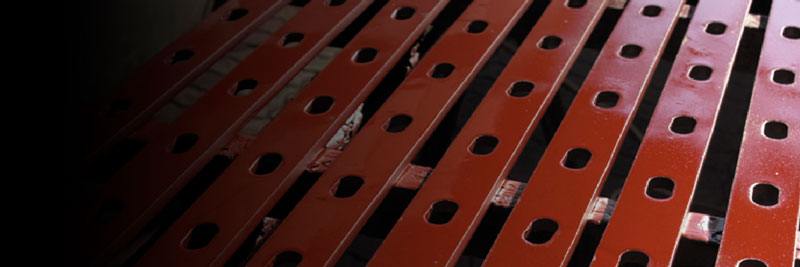
Expansion joint installation units are pre-fabricated installation sets that make installation much easier.
Expansion joints, pre-insulation layers and steel parts are fully pre-mounted and can simply be screwed or welded into the duct. In the event of system modifications, the installation unit can be removed and overhauled at our factory.
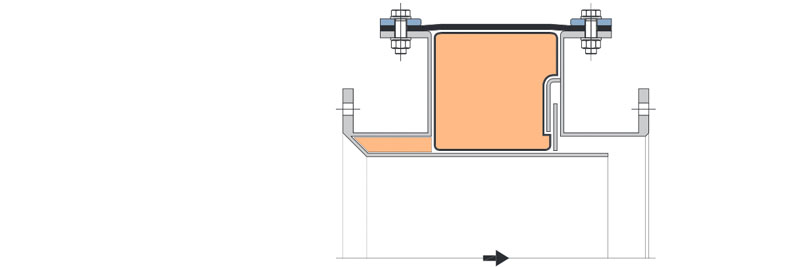
Our installation set contains all the tools and aids needed to close fabric expansion joints, including a PTFE welding tool. You can use it to weld a gas-tight sealing layer using PTFE film. With reference to our detailed assembly instructions that specially cover the closure of individual fabric layers, sealing films and external layers, any trained assembler will be able to close fabric expansion joints independently at the installation site.
The scope of delivery for expansion joints with installation seams includes the tools needed to close the expansion joint, such as sewing needles, thread and glue. If the installation set with PTFE welding tools is not ordered, the PTFE film is made endless by clinching.
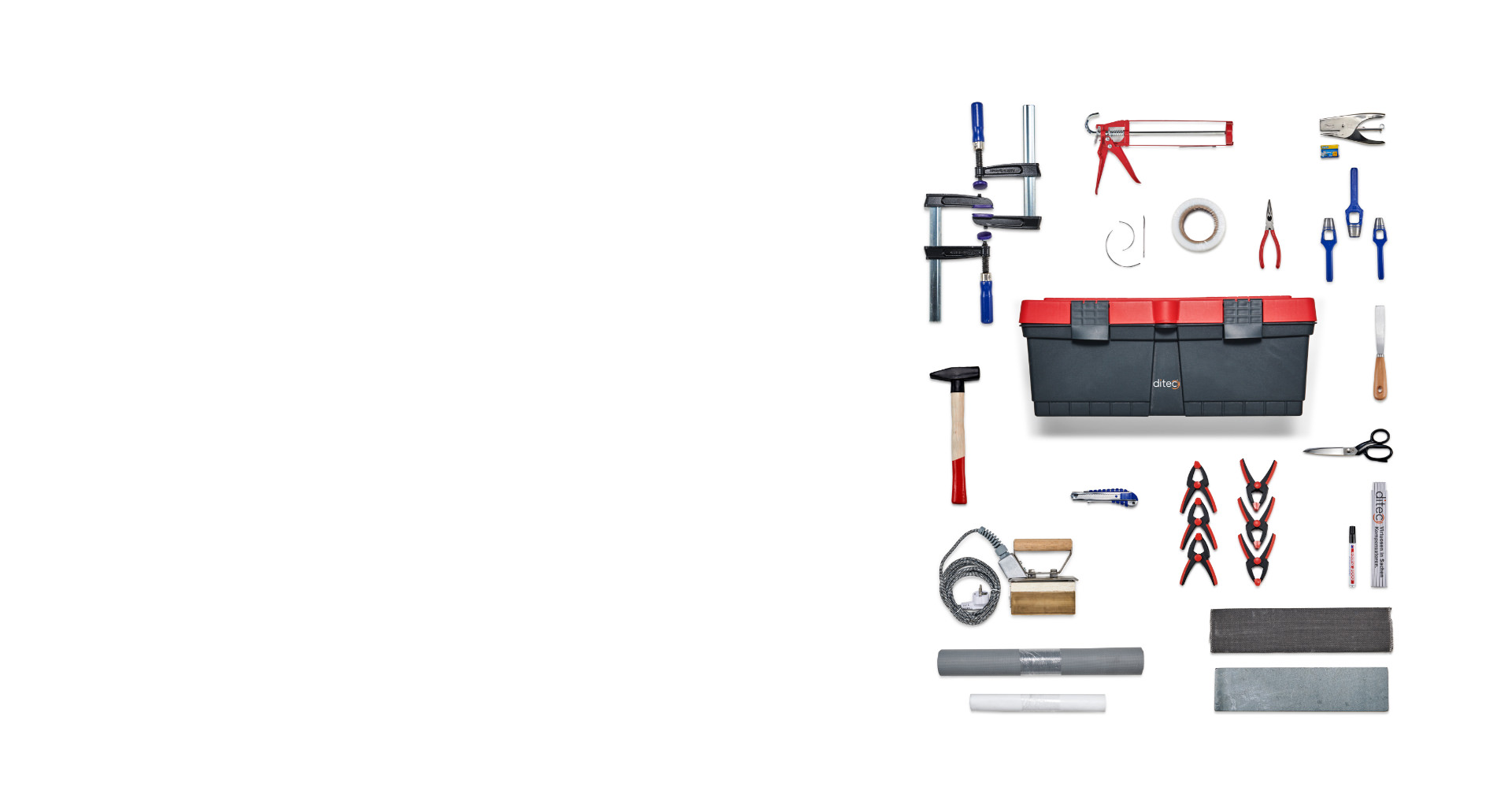
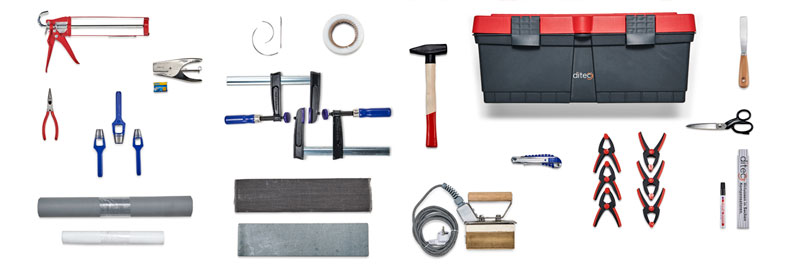